Deltia.ai's computer vision models are revolutionizing the shop floor by providing unprecedented visibility and actionable data. By capturing and analyzing thousands of data points, Deltia.ai identifies patterns and suggests areas for optimization, driving productivity and efficiency to new heights.
We’re exploring four different use cases where Deltia.ai's computer vision technology transforms operations: machine monitoring, manual assembly, material waste, and warehouse route optimization.
Enhanced machine monitoring
Manufacturers often face significant challenges with machine downtime, inconsistent quality, and high operational costs. Traditional Programmable Logic Controllers (PLCs) provide limited insights, often displaying cryptic error codes without context or detailed explanations. Older machines may lack the necessary sensors to track every component, making root cause analysis difficult.
Machine monitoring with Deltia.ai
Deltia.ai's computer vision technology enables the continuous tracking of machine states and components, identifying stoppages and generating video snippets for root-cause analysis. This enables maintenance teams to quickly diagnose issues and take proactive measures to prevent future downtime.
Operational anomalies
Deltia.ai can detect the most subtle of anomalies in a machine's operation, such as minute variations in a turning table's speed that indicate potential wear. By calling attention to these anomalies early, the Deltia.ai system calls attention to the need for predictive maintenance. Repairs and replacements can be planned and made before critical failures occur.
Quality issues
Deltia.ai also helps identify machine-based causes of inconsistent product quality. By monitoring production processes in real time, Deltia.ai identifies deviations from standard quality metrics and alerts operators to take immediate corrective actions. This ensures that every product meets quality standards, reducing rework and waste.
Energy and maintenance costs
Deltia.ai’s detailed insights into machine performance help optimize energy consumption and maintenance costs. By identifying inefficiencies and suggesting optimizations for machine operations, Deltia.ai helps manufacturers reduce energy usage and maintenance expenses, keeping production on track and limiting budget blowouts from unforeseen problems.
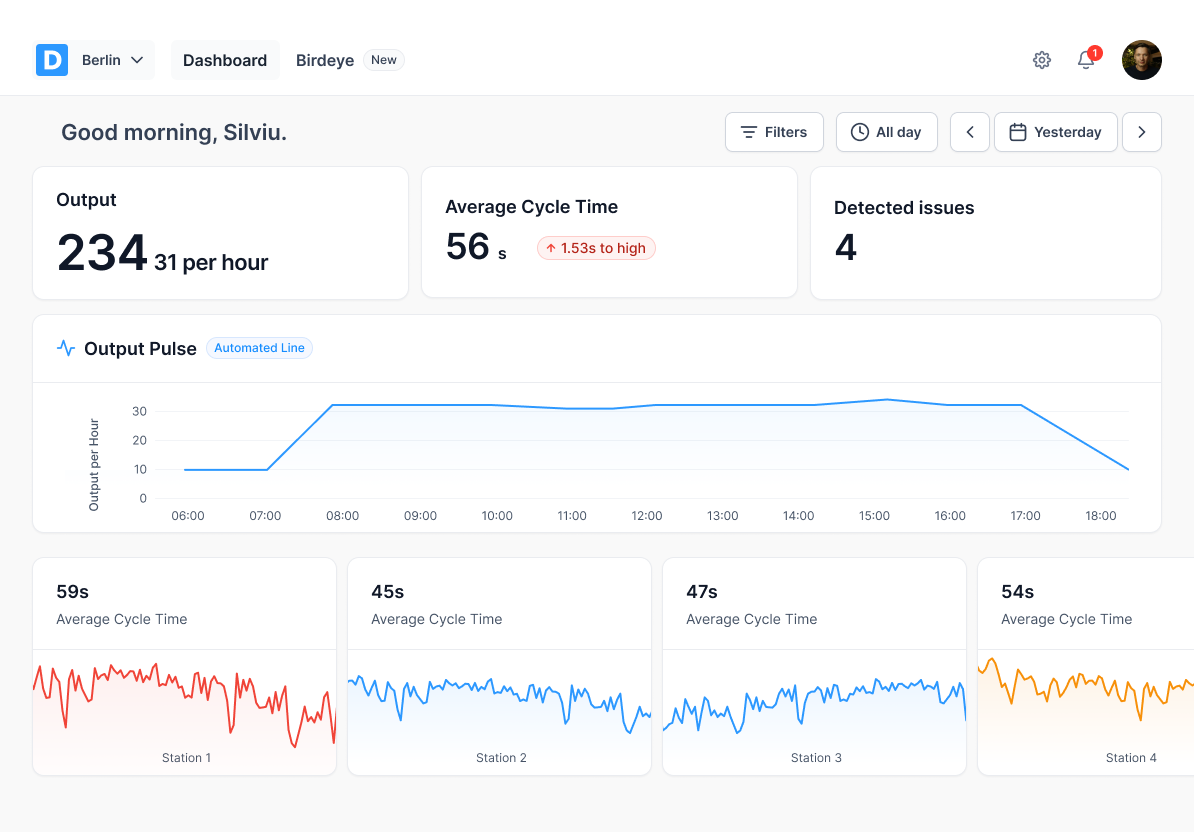
Streamlined manual assembly
Manual assembly processes often suffer from a lack of comprehensive data collection, leading to inefficiencies and errors. Without useful and accurate data, it’s hard to make informed decisions, or to identify where optimizations can be made. The shortage of skilled labor and high training costs further exacerbate these challenges.
Actionable insights, low costs
Companies that rely heavily on manual processes don’t necessarily have to spend a lot of time and money on digital transformation. By continuously monitoring manual processes, Deltia.ai captures and analyzes data from manual assembly operations, providing actionable insights into inefficiencies. This allows for workflow optimizations and error reduction, and identifies what’s already working well so best practices can be implemented across an organization.
Better training
Deltia.ai supports better training by identifying skill gaps and offering targeted suggestions for improvement, helping bridge the gap caused by labor shortages and lack of experience.
Real-time alerts
Deltia.ai can also quickly identify deviations from standard operating procedures and alerts operators in real-time. This minimizes errors and ensures that assembly tasks are performed correctly and efficiently.
Implementation of Deltia.ai has resulted in substantial productivity gains and cost reductions for manufacturers. Using Deltia, leading Swiss automation company ABB reported increased productivity, enhanced product quality, and reduced operational costs after implementing Deltia.ai on a number of its production lines. Since implementing Deltia.ai, ABB has seen a 15% increase in productivity. Deltia.ai customer Viessmann has also benefited significantly, with a 20% productivity increase at their Legnica plant, and expectations of up to 50% as Deltia.ai is deployed across more lines.
Minimizing material waste
Packaging errors and material waste are significant issues in the packaging process, leading to product damage, customer dissatisfaction, and increased costs.
By analyzing the use of materials and identifying areas of inefficiency, Deltia.ai enables manufacturers to reduce waste, contributing to sustainability efforts and cost savings. Deltia.ai monitors operations in real-time, identifying errors immediately so they can be corrected before they multiply.
Route optimization
Inefficient routing within warehouses leads to excessive travel time, delays, and increased operational costs. Poor inventory management further complicates these issues.
Efficient warehouse routes optimization
Deltia.ai analyzes warehouse layouts and workflows to optimize routing. By identifying the most efficient paths for movement, Deltia.ai reduces travel time and improves overall efficiency. This streamlined routing also enhances inventory management, reducing unnecessary movement and labor costs.
For example, Deltia.ai’s algorithms can suggest route adjustments based on real-time data, ensuring that warehouse operations are continuously optimized for maximum efficiency.
Transforming shop-floor visibility with Deltia.ai
Deltia.ai's computer vision models offer a depth of visibility into shop floor operations that was previously unattainable. Deltia.ai's computer vision technology is transforming manufacturing by providing deep insights and solutions for machine monitoring, manual assembly, material waste, and warehouse route optimization.
Interested in learning more about the substantial impact Deltia.ai can have on productivity, efficiency, and cost savings? Book time with one of our optimization specialists for an analysis of how Deltia.ai can work for you.